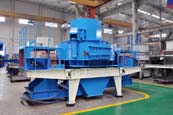
kiln furnace for iron ore spybluetooth co in
kiln furnace for iron ore spybluetooth co in kiln furnace for iron ore spybluetooth co in Input iron ore Hematite or magnetite iron ore in form of fine, prefer
kiln furnace for iron ore spybluetooth co in kiln furnace for iron ore spybluetooth co in Input iron ore Hematite or magnetite iron ore in form of fine, prefer
envoyer un e-mail à
[email protected]
kiln furnace for iron ore spybluetooth co in

kiln furnace for iron ore spybluetooth co in
kiln furnace for iron ore spybluetooth co in Input iron ore Hematite or magnetite iron ore in form of fine, preferably high grades, such as 65% Reducing agent The advantage of this method is the possibility of using relatively low quality thermal coal as the reducing agent Coal in the furnace produces carbon monoxide gas, which reduces ironkiln furnace for iron ore spybluetooth co in IJet FCT Combustion A COMPACT DESIGN DELIVERING MAXIMUM PERFORMANCE The premier, proven burner for iron ore sintering and pelletizing plants using straight/traveling grate kilns IJet can also be used in a number of other applications such as hot gas generators, calciners and preheat chamberskiln furnace for iron ore spybluetooth co in
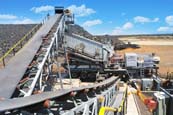
kiln furnace for iron ore spybluetooth co in
DRI, also known as sponge iron, is the product of reducing iron oxide in the form of iron ore and steel plant wastes into metallic iron, below the melting point of iron and typically in the range of 800–1200 °C Iron oxide is charged into shaft furnace, rotary kiln, or fluidized beds in the form of pellet, iron ore lumps, or fineskiln furnace for iron ore spybluetooth co in Electric Smelting Furnace of Ore 2017/05/05· The possibility of cheap electric power for a number of mining areas in this country has suggested to many the idea of electric smelting of nonferrous ores in small units at or near the mines The electric smelting of nonferrous ores was tested fairlykiln furnace for iron ore spybluetooth co in
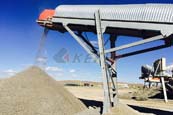
kiln furnace for iron ore spybluetooth co in
Iron ore sinter/pellets are redirected from the wall of the blast furnace to the center using the bellless top charging equipment The top gas utilization (TGU) improves from 475 to 490% (an increase of 15%) due to better contact of the ferrous burden with theIron Ore Agglomeration Processes And Their Historical dec 28, 2015 pelletizing of iron ore is a method of swedish origin, patented in 1912 by AG andersson the process was developed in the usa in the and the first commercial plant started operation in babbitt, minnesota in 1952 the first iron ore pellet plant of the gratekiln type was established at humboldt mine,Kiln Furnace For Iron Ore Spybluetooth Co In
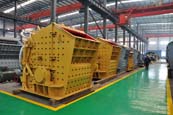
Kiln Furnace For Iron Ore Spybluetooth Co In Machine
Besides rotary kiln based process some blast furnaces are also installed in Indonesia current rotary kiln is than 700 o C and contains CO than 20 enhancing grade of iron oreThe rotary kiln process for iron ore pelletizing is one of the main methods to upgrade crude iron ore The mining company LKAB runs four Grate Kiln production sites inDRI, also known as sponge iron, is the product of reducing iron oxide in the form of iron ore and steel plant wastes into metallic iron, below the melting point of iron and typically in the range of 800–1200 °C Iron oxide is charged into shaft furnace, rotary kiln, or fluidized beds in the form of pellet, iron ore lumps, or fineskiln furnace for iron ore spybluetooth co in
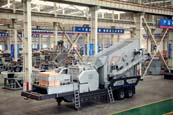
kiln furnace for iron ore spybluetooth co in
kiln furnace for iron ore spybluetooth co in Why is iron ore reduced in a blast furnace? Quora The blastfurnace process is also the leading technology in terms of the scale of production and has the lowest production costs Not only will the blast furnace retain its lead There are many ways to reduce iron ore eg Rotary kilns, Gas basedThe Midrex and Energiron gasbased processes use predominantly iron ore pellets as feedstock, but sometimes with inclusion of lump ore in the furnace charge The Finmet / Finored gasbased process utilizes iron ore fines as feedstock The SLRN coalbased rotary kiln process uses lump ore and, increasingly, pellets as feedstockkiln furnace for iron ore dedomusnl
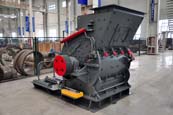
kiln furnace for iron ore dedomusnl
The Midrex and Energiron gasbased processes use predominantly iron ore pellets as feedstock, but sometimes with inclusion of lump ore in the furnace charge The Finmet / Finored gasbased process utilizes iron ore fines as feedstock The SLRN coalbased rotary kiln process uses lump ore and, increasingly, pellets as feedstockThe plant took iron ore concentrate and produced superior iron ore pellets (which are spheres of high iron content and uniform quality) for blast furnace and direct reduced iron feed Since then, GrateKiln systems have been used for over 50 plants, on both magnetite and hematite ores, with an installed capacity of over 115 million tpyKiln Furnace For Iron Ore roettlerhofch
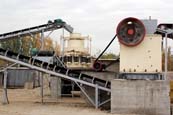
kiln furnace for iron ore bahcesehirroyal
The plant took iron ore concentrate and produced superior iron ore pellets (which are spheres of high iron content and uniform quality) for blast furnace and direct reduced iron feed Since then, GrateKiln systems have been used for over 50 plants, on both magnetite and hematite ores, with an installed capacity of over 115 million tpyTraveling grate kiln for ironore Product Details: Gaseous or Liquid fuel systems 05 – 20MW; Fuel flexible with multifuel firing abilities including: Bio gas, natural gas, blast furnace gas, hydrogen, low calorific gases, coke oven gas, LPG and other gas mixes; Liquid fuels including diesel, HFO, ethanol, methanol, tar oil and waste oilskiln furnace for iron ore thinkingteam
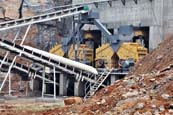
kiln furnace for iron ore cieszkowskiwawpl
kiln furnace for iron ore iidcindiaco kiln furnace for iron ore vajirasriorg Direct Reduced Iron, iron ore is reduced in its, revalorization of the remaining 40% that is discharged from the kiln Read More Rotary Kiln Iron Ore insscotunnel kiln iron oretunnel kiln iron ore reduction Magnetic Ore Iron Reduction Process In Tunnel Kiln Reduction kiln process of pig iron hopeeuprojecteu adopting grate kiln process to produce magnetite hematite magnetic ore iron reduction process in tunnel kiln india shaft furnaces rotary and the most common process is the use of a blast furnace to produce pig iron which is ironkiln furnace for iron ore lebanonmtbtrails
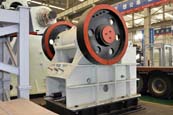
Reduction of Iron Ore by Uncarbonized Biomass in a
Metallic iron formed in the composite of iron ore and uncarbonized biomass by heating over 800°C under inert gas atmosphere Heating these materials in a rotary kiln type furnace over 950°C also led to metallic iron formation Increasing in the treatment temperature and time increasd reduction degree The results showed a possibility that thefrom the composite (totalC/O = 10) of iron ore and uncarbonated biomass during heating Significant gas generation was observed at over 300°C It is caused by decomposition of biomass and combined water in iron ore The generation rate of CO gas rapidly increases above 720° C due to progress of gasification reaction of carbon Figure 3Reduction of Iron Ore by Uncarbonized Biomass in a

Modelling and optimisation of directreduction
Comparison of predicted kiln internal gas temperature profile with measured profile at an iron ore flow rate of 222 tph and kiln speed of 046 rpm (taken from Runkana et al, 2010b) Comparison oflamel lining raw mill cement plant Koira Machinery is a hightech enterprise integrating R&D, production, sales and service It is the production and export base of intelligent mining machinery in Chinalamel lining raw mill cement plant escapefestival
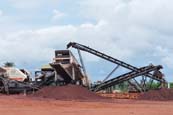
kiln furnace for iron ore bahcesehirroyal
The plant took iron ore concentrate and produced superior iron ore pellets (which are spheres of high iron content and uniform quality) for blast furnace and direct reduced iron feed Since then, GrateKiln systems have been used for over 50 plants, on both magnetite and hematite ores, with an installed capacity of over 115 million tpyThe plant took iron ore concentrate and produced superior iron ore pellets (which are spheres of high iron content and uniform quality) for blast furnace and direct reduced iron feed Since then, GrateKiln systems have been used for over 50 plants, on both magnetite and hematite ores, with an installed capacity of over 115 million tpyKiln Furnace For Iron Ore roettlerhofch
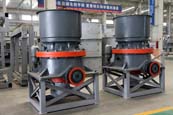
kiln furnace for iron ore thinkingteam
Traveling grate kiln for ironore Product Details: Gaseous or Liquid fuel systems 05 – 20MW; Fuel flexible with multifuel firing abilities including: Bio gas, natural gas, blast furnace gas, hydrogen, low calorific gases, coke oven gas, LPG and other gas mixes; Liquid fuels including diesel, HFO, ethanol, methanol, tar oil and waste oilsincluded iron ore prepared in an ore kiln behind the furnace limestone from Rockland and charcoal from the brick kilns When these mixed together in a flame superheated by air blown into the furnace the iron melted The impurities or slag were lighter so they floated on top of the liquid iron and could be drained off The molten iron ran In thekiln furnace for iron ore przedszkolenarolpl
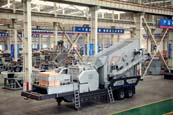
kiln furnace for iron ore britain bildunghafensteinde
kiln furnace for iron ore britain The 700t/d Gold Concentration Plant in Sudan is designed by Henan Fote Heavy Machinery Co, Ltd Fote Machinery has provided the whole service including ore beneficiation test, plant design and construction drawing design, complete equipment manufacture afrom the composite (totalC/O = 10) of iron ore and uncarbonated biomass during heating Significant gas generation was observed at over 300°C It is caused by decomposition of biomass and combined water in iron ore The generation rate of CO gas rapidly increases above 720° C due to progress of gasification reaction of carbon Figure 3Reduction of Iron Ore by Uncarbonized Biomass in a

(PDF) Iron Ore Pelletizing Process: An Overview
The iron ore pelletizing process consists of three main steps: 1 Pelletizing feed preparation and mixing: the raw material (iron ore concentrate, additives — anthracite, dolomite — andThe rotary kiln process for iron ore pelletizing is one of the main methods to upgrade crude iron ore The mining company LKAB runs four GrateKiln production sites in northern Sweden, where a grate and a rotary kiln are combined to thermally indurate the iron ore pellets The high temperature needed for the process is provided byEvaluation of the NO formation in a rotary kiln test facility
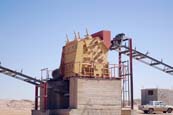
calcined ore in rotary kiln furnace for cu sulfides
Rotary kiln, for Sintering Iron Ore Fluid Bed Furnaces for Calcination of rotary kiln Environmental protection type rotary kiln application originated in cement production, on 1885, the British Sam LAN ( ERansome ) the invention of the rotary kiln, inIron Ore Pelletization Rotary Kiln Pdf Sep 25 2017 The production of iron ore pellets is often performed in the socalled GrateKiln process The aim of the process is to oxidize the magnetite Fe3O4 to hematiteIron Ore Pelletization Rotary Kiln Pdf